Leadership
A Global Commitment to Premium Quality
As Henry Timken was passing his business on to his sons in 1899, he advised them, “If you want to lead in any line, bring to it … unfailing industry, aggression and indomitable purpose.”
That entrepreneurial mindset no doubt helped young W.R. and H.H. Timken take the newly developed tapered roller bearing technology to the market and build a thriving business.
Today, it’s fair to say those who know bearings know the Timken name — and associate it, invariably, with premium quality. Even as the company has expanded around the world and grown its product offerings and areas of expertise, that quality ethos remains central to the identity of every Timken associate.
Taking challenging applications to heart
As VP of Quality, Matt Eckels carries that ethic into the next decade, traveling the world to protect the integrity of the Timken brand as associates undergo training, build new factories and develop new products.

Matt Eckels, vice president, leads The Timken Company’s global quality efforts.
Eckels doesn’t consider himself a traditional quality expert, although he has spent nearly 20 years at Timken. With a background in application engineering and product management, he brings to his role a strong customer focus and an understanding of how to deliver Timken solutions that satisfy customer needs.
“Quality standards and expectations at Timken are very high,” he says, “because we participate in challenging markets that require highly engineered, reliable, premium-quality solutions.”
While customers expect products that can rise to any challenge, product launch cycles continue to shorten as manufacturers look to be the first out with the next big technological advancement. “We’re seeing aggressive timelines in many markets, but high quality remains a given,” says Eckels.
Because of advancements in artificial intelligence, autonomous operation and alternative fuels, for example, agricultural implements today may see shorter production timelines and shorter lifespans than ones produced 50 years ago. During those shorter lifespans, however, manufacturers and customers expect to see zero performance issues.
“Every day, when the farmer goes out to work in the field, that tractor needs to perform — and in sometimes unforgiving environments,” says Eckels.
The same goes for the wind industry, where replacing the main shaft bearing in an offshore turbine costs several hundred thousand dollars. Those bearings must last up to 25 years in some of the harshest conditions imaginable.
Plant managers in the food and beverage industry, on the other hand, require premium bearings even when they change them out routinely every six months. Bearing failure for them means the risk of food contamination, brand degradation or, at the very least, lost revenue when plant operations come to a standstill.
Quality and reliability are also critical in aerospace applications, where the safety of operators and passengers rests on a landing wheel bearing or a helicopter transmission.
Timken engineers take those challenges to heart and it brings out the best in them, says Eckels. “We excel in mission-critical applications because of our strong commitment to being the best — and to leaving no stone unturned when it comes to building machines that people can depend on.”
Managing quality on a global scale
Eckels says Timken engineers also excel at optimizing and predicting bearing performance because they have the tools to empirically test and validate it. “If we put something in a catalog, whether it’s a rating or a load maximum, we’ve calculated it precisely, and we’re sure it’s 100% accurate,” he says.
That promise applies to all Timken-branded products, wherever in the world they’re made. Timken associates at every level of the organization follow the Timken Quality Management System (TQMS), which outlines clear guidelines for acceptable and exceptional levels of quality standards.
“Whatever the function, whether it’s product engineering, application engineering or customer service, they all follow this system,” says Eckels. “It applies to all our facilities around the world, as well as to local and global suppliers.”
The 21 modules in the TQMS pyramid are based on best practices of multiple industry quality systems. TQMS modules work together to evaluate the risk of Timken products falling below acceptable standards and to continually manage, track, address and reduce that risk.
At the heart of the TQMS system is a digital platform that brings cutting-edge software tools to bear, adding rigor to TQMS processes, streamlining collaboration and shortening response times.
“That investment in digital helps us be more effective and efficient so we can respond to customers more quickly,” says Eckels.
One company. One standard.
As Timken teams plan and build new facilities, they design systems and infrastructure that capture the importance that quality plays in the business. “It’s part of the culture from the very beginning,” says Eckels.
He spends a lot of time visiting Timken facilities around the world and is continually impressed by that culture of quality. “No matter where I go, it’s the same,” he says. “There may be differences in how we serve customers or in our sales and supplier interactions — but from a quality perspective, we’re all speaking the same language.”
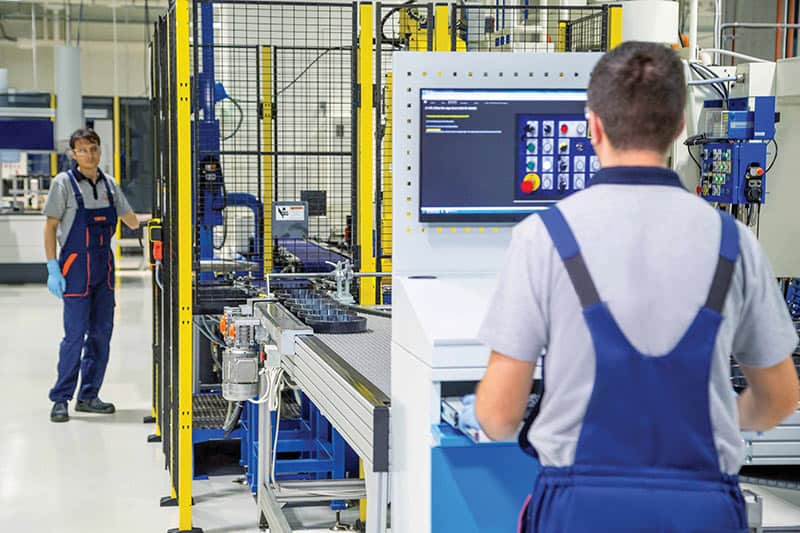
The new facility in Prahova, Romania, demonstrates Timken’s ongoing commitment to quality in every corner of the world.
Eckels is charged with making sure that global standard flows consistently into every product, wherever it is made. Every year, his team gathers products from Timken facilities around the world, brings them back to headquarters and runs them through a battery of tests.
“We’re the only bearing company in the world, that I know of, that performs that kind of audit on a regular basis,” he says. “No matter where it’s produced—what we say we’re going to deliver, we deliver. Whether your bearing comes out of Ohio or China — it’ll be the same.”
For Timken associates around the world, achieving consistent quality standards is a matter of pride as well as healthy competition. Every year, each facility is charged with meeting or exceeding a set of metrics, continually improving their output from the previous year. Those who achieve the goals set for them receive the coveted Timken Foundation Quality Excellence Award.
“It really gets to the core of what we’re trying to do, and how our facilities and our people are invested in quality and what it means for the company,” says Eckels.
The dynamic duo: Quality + Growth
Timken’s Quality team also plays a role as the company expands through acquisitions. Timken has a history of buying premium brands, and Eckels’ team stands ready to help them evolve to the next level of quality and performance. “As those companies are integrated into the Timken family of brands, the company supports them through capital investments, knowledge sharing and best practices,” he says.
Eckels views his role as both the protector of the Timken brand and as a leader in its evolution. To meet rising expectations, he says teamwork is essential, along with continued digital and process advancements. “We partner closely with business leads to understand how we are going to get there together,” he says.
Eckels makes sure his team is involved early on with any new Timken plant, product or process. He is setting up his global organization to be increasingly proactive in their work, teaming up with Timken facilities and suppliers to catch quality risks before they can cause problems.
“Our reputation for quality—the reliability and efficiency of our products — that’s what customers think of when they hear the Timken name,” he says. “Today, my team is defining how we build on that reputation in the context of the 21st century.”
Learn more about how Timken measures quality and see our global Quality Registrations.
Last Updated: 2021/08/19
Published: 2020/01/23