Efficiency
Solving for Early Failure in Mainshaft Bearings
Why the TDI is a Wind Energy Favorite
As the wind energy industry grows, so does demand for the parts and services that make it possible. Timken investments in wind over the past 15 years are paying off for the company, with wind energy revenue growing to 17% CAGR over the past 5 years, more than double the industry growth rate.
Timken serves the industry through a variety of products, like coatings, lubrication systems and torsional control products. Engineered bearings play a central role in their wind energy work however, with the Tapered Double Inner (TDI) Mainshaft Roller Bearing being a leading recommendation.
We spoke with Caleb Chovan, principal application engineer supporting the wind energy sector, to get his thoughts on why the TDI is such a change-maker.
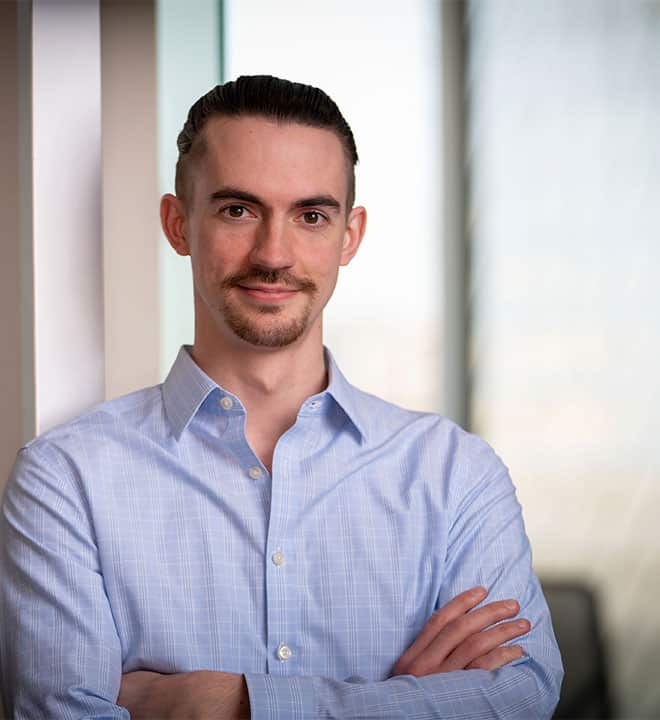
“One of the best things about my job is having the freedom to design and bring new and innovative products to market.” Caleb Chovan, principal mechanical engineer
Q: Why was the TDI bearing originally developed for wind turbines?
Chovan: The TDI grew out of a major problem that the industry was facing. Many original equipment (OE) solutions came with a spherical roller bearing (SRB) for the mainshaft, and when turbines reached 1.5MW in size, those bearings started failing much earlier than planned.
Replacement was extremely expensive, sometimes involving a $150,000 crane service fee — a massive unplanned expense to any company trying to make money off of a wind turbine that was supposed to last 20 years, but which failed at six or eight.
One of our customers, a wind power producer in the United States, had a huge number of those turbines installed on wind farms in different parts of the country. Our engineers worked with them to develop a tapered roller bearing that could replace the original spherical bearing and provide improved performance.
Q: Timken engineers have received awards for their coatings work. Why not just put a coating on a replacement SRB?
Chovan: The Timken ES302 coating can significantly extend bearing life without changing the bearing design, and that’s certainly an option for mainshaft bearings. The protective coating adds a second line of defense to slow down the wearing process caused by slippage between the rollers and the raceway. That slippage causes excessive wear of the bearing race and can cause early bearing failure.
Replacing the SRB with a TDI, on the other hand, is designed to eliminate roller slippage and lengthens gearbox bearing life as well. SRBs, by design, have a small amount of play in them, which can lead to a floating mainshaft that can move axially. When it moves too much, it puts unintended loads into the gearbox, which sits right behind the mainshaft bearing.
When we switch over to a TDI, we can create a rigid system with no play in the bearing at all — essentially locking that bearing in place and forcing it to carry all the loads it’s designed to carry. So, none of those loads get transferred to the gearbox bearings. We work with customers to decide which solution makes the most sense for their use case.
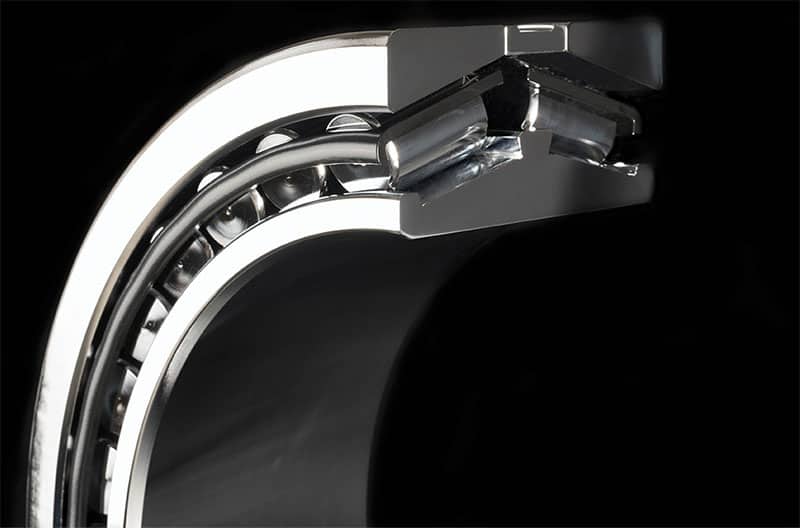
The TDI bearing is designed to eliminate roller slippage in wind turbine mainshafts.
Q: How have TDI bearings stood up in the field over time?
Chovan: We inspected one prototype after it had run for two years, and it was in great condition — looked almost brand new. Two others were recently removed after five-and-a-half years of runtime because the turbines they were running in were upgraded with larger-megawatt equipment. Early data indicates these bearings would have lasted much longer than the original OE bearings had the equipment not been upgraded.
The industry is undergoing continual, transformative change, so it can take a long time to prove out a new technology. What’s clear is that Timken TDIs have become more popular with our wind energy customers, who increasingly use them to replace failed bearings across their turbine fleets.
Along those lines, we’re currently working on a new version of the TDI that will transform turbine maintenance processes in the field. I’m really looking forward to talking more about that with customers.
Q: What’s it like to work in the wind energy field, at this point of history?
Chovan: It’s a really young industry — and growing so fast. Global electricity generated from wind was up 11 percent in 2020. Everyone’s racing to figure out the best solutions, so it’s both incredibly challenging and rewarding to contribute to all those competing ideas that are helping to bring more emission-free power to more homes and businesses around the world.
It’s been fun to watch: As costs come down, more investment rolls in, and suddenly here we are, with an industry that makes sense not only from a climate perspective, but from a business viability perspective, as well.

Last Updated: 2021/08/13
Published: 2021/05/13