Innovación
El material adecuado para cada aplicación
Antes de llegar a la empresa hace cinco años, la experiencia de Lee Rothleutner con Timken se limitaba al rancho en Nebraska donde creció. La caja negra y naranja era algo común en el banco de trabajo mientras él y su padre cambiaban los rodamientos del tractor.
Después de comenzar en el departamento de Investigación y Desarrollo (I+D) de Timken, la perspectiva de Rothleutner cambió notablemente. “Me di cuenta exactamente de la amplitud del trabajo que hace Timken”, afirma. «Soy un metalúrgico con un doctorado y no hay nada más emocionante que tener acceso a laboratorios donde puedo realizar casi cualquier proceso de tratamiento térmico de metales que desee».
Hoy, como responsable de I+D de materiales, Rothleutner aporta esa mentalidad a su equipo. “Saco este libro enorme de mi estante, Manual de ASM, volumen cuatro”, comenta. ASM International es la comunidad mundial de ingenieros de 108 años de antigüedad conocida por recopilar y difundir conocimientos sobre materiales. El volumen cuatro se titula Tratamiento térmico.
«Les digo que quiero que tengamos una posición en cada proceso de tratamiento térmico en ese libro», afirma: “Si funciona o no para nosotros y por qué. Si funciona, quiero el proceso y los medios para poder implementarlo «.
Los ingredientes de una marca de ingredientes
Inicialmente, Rothleutner fue contratado para ayudar a impulsar el desarrollo del proceso de endurecimiento por inducción sin fisuras de Timken para rodamientos del eje principal de turbinas eólicas de diámetro ultra grande. Tuvo un gran éxito allí y fue ascendido a liderar el grupo de conversión de materiales antes de asumir su puesto actual.
Como resultado de su trabajo en energía eólica, Rothleutner pasó mucho tiempo en Rumania, trabajando con el equipo del Centro de excelencia de ingeniería en Ploiesti. Hoy en día, él y su equipo también desempeñan un papel en los avanzados procesos y tecnologías de templado que se presentan en las cercanías de la planta de Prahova. “Allí, utilizamos un proceso llamado ‘austempering’ (temple austenítico) que produce acero bainítico”, sostiene.
El equipo también ha avanzado con tecnologías de recubrimientos en los últimos años, duplicando la capacidad en 2020. “Existe una gran demanda para eso en este momento, y Vikram Bedekar, nuestro líder de grupo en esa área, ha hecho un trabajo tremendo”, afirma Rothleutner.
El equipo de materiales también se encarga de optimizar los procesos de cementado, una tecnología que se remonta a la patente original de Timken de 1897. “Conocemos esa tecnología muy bien, por lo que sabemos dónde puede implementarse y cuándo son más adecuados otros procesos”, sostiene Rothleutner.
Ingrediente correcto, aplicación correcta
Las soluciones de ingeniería de Timken implican, en la raíz, identificar los ingredientes correctos y la receta adecuada para cada aplicación. “Los clientes vienen a nosotros con un conjunto específico de propiedades que quieren alcanzar”, afirma Rothleutner. «Juntamos la química y la estructura».
Llegar allí es un esfuerzo de equipo, con ingenieros de aplicaciones a la cabeza. El equipo de I+D se involucra cuando la solución requiere una química y una estructura que van más allá de los procesos estándar de Timken, pero la elección de los materiales a menudo se reduce a las condiciones de la aplicación. Las aplicaciones que tienen las cargas de impacto y los escombros más duros, como líneas de fundición continua en las acerías, requieren acero cementado, el más duro de los duros. Para aquellos con buena lubricación en ambientes menos extremos, el acero bainítico puede funcionar igualmente bien.
Hoy, por ejemplo, un fabricante de equipos de minería y construcción está convirtiendo los rodamientos diferenciales de Timken en cargadores de ruedas de acero cementado a acero templado. Las transmisiones de implementos agrícolas también cuentan cada vez más con rodamientos templados.
“Aprovechamos nuestro siglo de experiencia con el proceso de cementado para comprender las limitaciones de los diferentes procesos”, sostiene Rothleutner. «Tenemos las pruebas, tenemos los datos, por lo que sabemos exactamente cuándo otros procesos pueden proporcionar un rendimiento igualmente alto con menos recursos».
En el caso de los rodamientos del eje principal de las turbinas eólicas, los ciclos del proceso de cementado habrían agregado 100 horas o más al proceso de fabricación, mientras que el endurecimiento por inducción sin fisuras hace lo mismo en aproximadamente dos horas. “Estamos hablando de una reducción del 50 % en el tiempo de producción de un rodamiento, por lo que los clientes lo escriben cada vez más en sus especificaciones”, afirma.
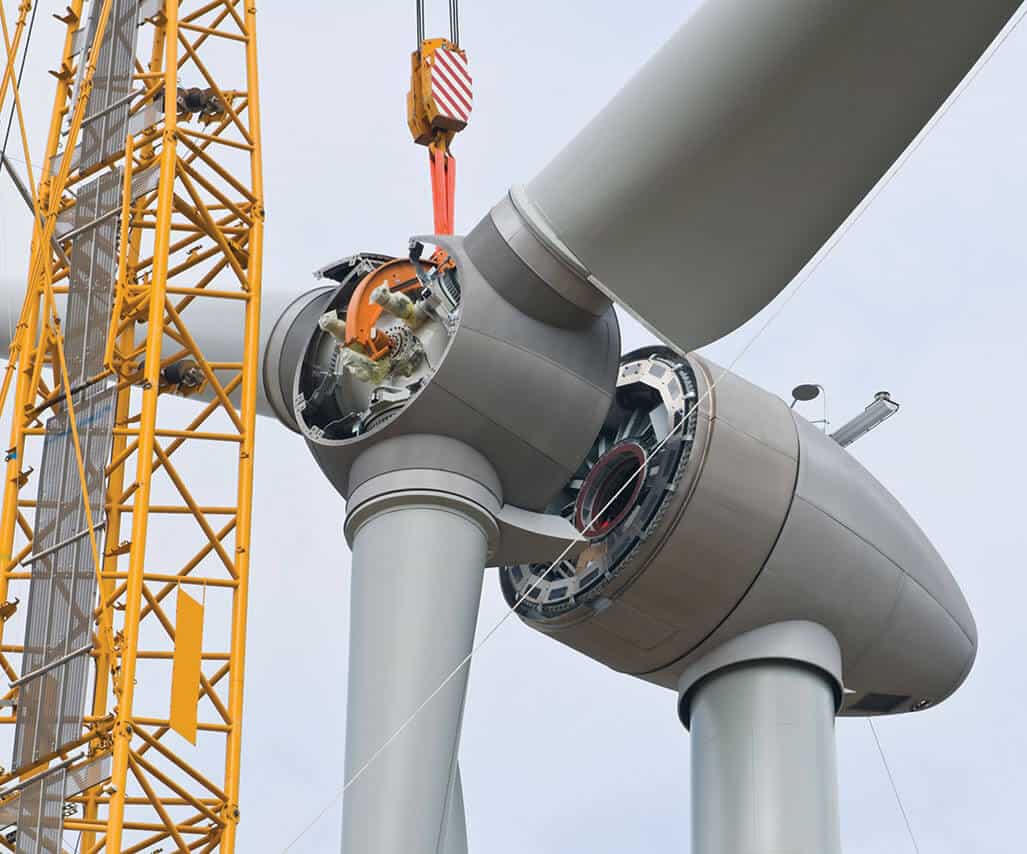
Me enorgullece mucho mi trabajo en el sector de las energías renovables y sé que ha sido un gran impulsor para muchas de las personas que he contratado. Los amigos de algunas de las empresas de energías renovables más conocidas del mundo están asombrados por el trabajo que hacemos aquí con turbinas eólicas y rodamientos terriblemente grandes. Conocen los desafíos allí.Lee Rothleutner
gerente del departamento de I+D de materiales
Modelado avanzado, soluciones más rápidas
El equipo también está evaluando las capacidades de fabricación de aditivos de metales en 3D, utilizando impresoras 3D para crear prototipos, piezas de demostración y componentes de herramientas personalizados. “El 3D es un tema candente en la industria y estamos evaluando dónde encaja exactamente para nosotros”, dice Rothleutner.
Por ahora, el mayor beneficio proviene del esfuerzo del equipo por avanzar en el modelado de procesos y elementos finitos. “La recopilación de datos sobre nuestros procesos de tratamiento térmico nos ayuda a ser más predictivos, a diseñar una solución antes de hacer un prototipo sólido y predecir cómo se comportará el producto en el futuro”, afirma.
El modelado avanzado también ayuda al equipo a interactuar más directamente con los clientes, para que puedan comprender los matices de las aplicaciones con mayor claridad y encontrar soluciones más rápidamente.
Una comunidad metalúrgica
La investigación de materiales es compleja, pero también es muy gratificante para un grupo de personas que disfrutan de lo que sucede cuando se combinan la química, la estructura y las propiedades en un laboratorio donde cualquier día promedio podría implicar un gran avance metalúrgico.
“En este momento, estamos trabajando para optimizar nuevos procesos de cementado y nitruración por plasma, y otros proyectos divertidos para diferentes segmentos del negocio”, sostiene Rothleutner. «Estamos buscando cajas de engranajes de turbinas eólicas, algunas aleaciones aeroespaciales, algunas soluciones todoterreno para condiciones extremas».
Los flujos de trabajo en constante evolución y la sensación de participar en proyectos que aumentan la eficiencia y el progreso los mantienen comprometidos para regresar al laboratorio todos los días.
El equipo de I+D de Timken trabajó directamente con los clientes para desarrollar recubrimientos resistentes al desgaste ES302. Lea cómo los resultados extienden notablemente la vida útil de las aplicaciones en energía eólica, agricultura, aeroespacial y otras.
Last Updated: 2021/06/9
Published: 2021/05/24